Understanding the Specifications for Welding Inspection Gilbert Arizona: A Full Overview
Understanding the Specifications for Welding Inspection Gilbert Arizona: A Full Overview
Blog Article
A Comprehensive Guide to Welding Evaluation: Comprehending Criteria, Techniques, and Finest Practices for High Quality Guarantee
Welding examination plays an essential duty in ensuring the structural stability and safety and security of bonded elements, requiring a thorough understanding of sector criteria such as those developed by AWS and ASME. Different evaluation methods, including ultrasonic and visual screening, are used to find prospective flaws that might compromise top quality. Implementing best practices can dramatically improve operational integrity and foster count on among customers. As we explore these critical components, it comes to be apparent that the effects of welding assessment extend much beyond conformity, inviting a more detailed assessment of how these processes shape industry requirements and practices.
Relevance of Welding Evaluation
Welding assessment plays an essential function in making certain the integrity and safety and security of bonded structures. It is a necessary procedure that validates that welds adhere to predefined specs, which is essential in numerous industries, consisting of building, vehicle, and aerospace. By carrying out comprehensive inspections, prospective problems such as splits, incomplete combination, and porosity can be identified early, avoiding disastrous failings that can bring about crashes or pricey repairs.
The importance of welding evaluation prolongs beyond simple compliance with policies; it likewise fosters count on with stakeholders. Clients and regulatory bodies expect assurance that the structures they depend on are built to withstand functional stress and anxieties. In addition, reliable welding assessment methods contribute to long-lasting toughness and performance of the structures, ultimately bring about minimized maintenance costs.
Additionally, welding examination advertises a culture of quality within companies, urging adherence to best techniques and constant enhancement. By incorporating assessment processes right into the welding process, companies can boost their track record and establish themselves as leaders in top quality assurance. Finally, the importance of welding inspection depends on its capability to safeguard lives, make sure structural dependability, and copyright industry requirements, making it an indispensable facet of welding operations.
Secret Industry Criteria
Making sure compliance with crucial industry requirements is vital for preserving the top quality and safety of bonded frameworks. Various companies develop these standards to promote ideal practices in welding and assessment - Welding Inspection Gilbert Arizona. Amongst the most acknowledged are the American Welding Culture (AWS) and the American Society of Mechanical Engineers (ASME), which supply detailed guidelines and specs for welding procedures and inspection criteria
AWS requirements, such as AWS D1.1 for architectural welding, rundown requirements for materials, style, and screening to make certain the honesty of welds. Similarly, ASME codes, including ASME Section IX, regulate the credentials of welders and welding treatments, guaranteeing constant top quality in commercial applications. Worldwide, the ISO 3834 standard emphasizes quality requirements for fusion welding, providing a framework for organizations to show conformity with worldwide finest methods.
Conformity with these requirements not only enhances the reliability of welded frameworks yet additionally mitigates risks related to architectural failings. Adherence to market standards is frequently a requirement for governing approvals and can significantly affect task specs. Eventually, understanding and executing these key criteria are vital for effective welding inspection look at these guys and quality control.
Inspection Techniques Review
Efficient welding inspection relies upon a range of techniques made to evaluate the quality and stability of welds. These techniques can be extensively categorized right into destructive and non-destructive screening (NDT) methods. Non-destructive screening techniques, which are commonly preferred in the sector, permit the examination of welds without compromising the stability of the material.
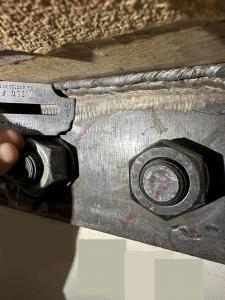
Among the most typically utilized NDT techniques are visual examination, ultrasonic testing, radiographic screening, and magnetic bit testing. Visual assessment is usually the initial action in the analysis procedure, making it possible for assessors to a knockout post recognize surface area flaws and examine weld grain profiles.
Each technique has its own advantages and restrictions, making it vital for examiners to choose the most appropriate approach based upon the certain demands of the project, the materials involved, and the urgency of the welds being evaluated. This mindful choice guarantees extensive assessments and promotes safety and security and top quality requirements in welding operations.
Usual Issues and Their Ramifications
A complete understanding of common flaws in welds is important for maintaining architectural integrity and safety and security in bonded constructions. Welding issues can substantially jeopardize the mechanical residential or commercial properties of the joint, leading to failings that could jeopardize both workers and equipment.
Typical issues consist of porosity, which manifests as little gas pockets trapped in the weld steel, compromising the total structure. Fracturing is another widespread issue, commonly resulting from fast cooling or incorrect joint layout, resulting in stress and anxiety concentrations that can cause catastrophic failings. Incomplete combination takes place when the weld metal stops working to properly bond with the base material, producing powerlessness that may cause splitting up under lots.
Other significant defects include damaging, where the weld grain erodes the base metal, and slag additions, which can prevent the weld's look at this site strength. Each of these problems has particular effects; for circumstances, porosity can reduce ductility, while breaking straight influences tensile toughness. Identifying and understanding these problems during assessment is essential for ensuring and implementing corrective steps compliance with market requirements, eventually protecting the architectural stability of bonded assemblies.
Finest Practices for Quality Control
Executing finest practices for quality assurance in welding procedures is vital for attaining ideal results and reducing problems. One crucial method is the establishment of clear welding procedures that stick to market criteria and requirements. These procedures ought to include detailed guidelines pertaining to product choice, joint preparation, and welding strategies to make sure uniformity and high quality.
Routine training and certification of welding employees are likewise important. Competent welders who recognize the relevance of quality control are more probable to generate sound welds. Additionally, carrying out a robust inspection program, consisting of both visual and non-destructive testing (NDT), can aid determine flaws early at the same time, enabling prompt corrective activities.
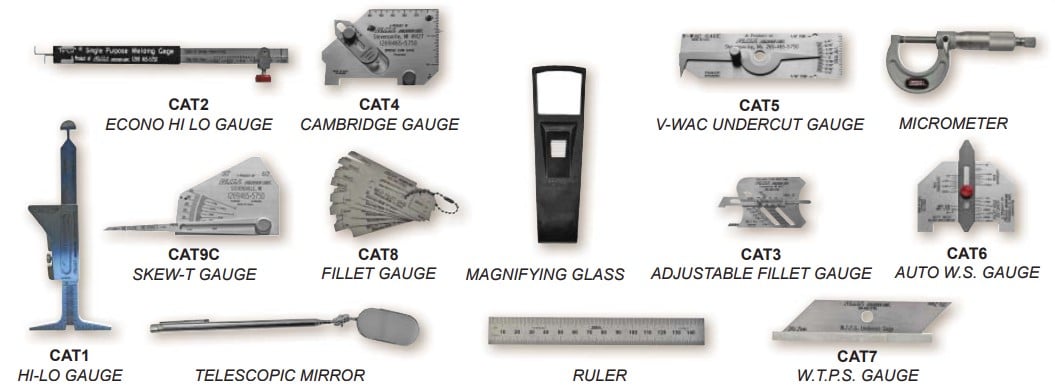
Last but not least, fostering a culture of high quality within the company urges employees to prioritize quality in their work. By adhering to these finest techniques, companies can boost the integrity of their welding processes, ultimately causing boosted item quality and reduced costs connected with rework and repair work.

Verdict
In conclusion, welding inspection plays an essential duty in making sure the integrity and safety of bonded structures. By implementing finest practices, companies can boost integrity, minimize maintenance prices, and cultivate trust among clients, inevitably adding to successful welding operations.
Additionally, welding inspection promotes a culture of high quality within organizations, motivating adherence to ideal methods and continual improvement. In verdict, the importance of welding examination lies in its capability to guard lives, guarantee architectural reliability, and support sector standards, making it a crucial aspect of welding procedures.
Amongst the most recognized are the American Welding Society (AWS) and the American Culture of Mechanical Engineers (ASME), which offer thorough standards and specifications for welding processes and assessment standards.
Ultimately, understanding and executing these crucial criteria are important for efficient welding assessment and top quality guarantee.
Effective welding inspection depends on a range of strategies made to assess the quality and integrity of welds.
Report this page